Design Support Services can also be integrated with our Manufacturing and Assembly Services.
- Implement a technical specification from concept to detailed drawings
- Provide technical analysis of drawings to investigate design-for-manufacturing efficiencies
- Build prototype and pre-production samples
- Provide dynamic simulation and test
- Projects at the initial design phase – from customers’ concept ideas or specifications
- Projects that require Design For Manufacture (DFM) assessment
- Re-design projects to enhance a product’s functionality, reduce costs, or resolve performance issues.
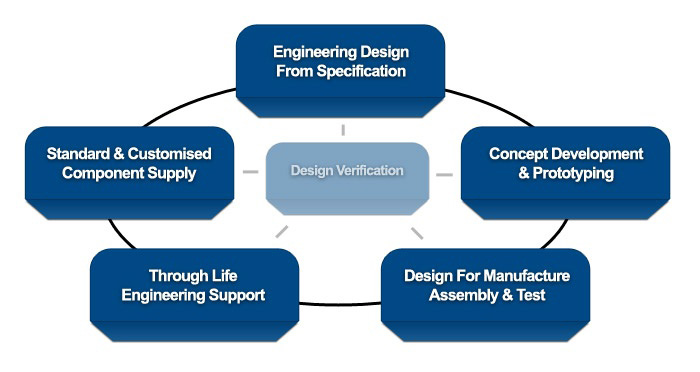
Re-Design For Mature Product Lines
We offer our design service to support mature products as well as new product concepts. At maturity, when production volumes begin to decrease, undertaking a re-design programme may help achieve critical cost reduction targets, alternatively, designing in a new feature to enhance the product may increase sales and extend the life of the product. We work to support our customers’ own designs, typically where the customer retains the IPR. We are able to undertake either a standalone design project, against a requirement specification, or, to work as part of a joint design team. This may be in response to our customers having identified a requirement and triggering the design project, or where we have been part of the manufacture or assembly process over a period of time and have made a design proposal to them, e.g. having identified an opportunity to reduce costs, improve performance or serviceability.
Design For Manufacture
Design for manufacture (DFM) is increasingly recognised by our customers as an important factor in reducing a product’s through-life cost. DFM activity can reduce cost by: mitigating risk, improving yield rates, reducing part count, easing the assembly process and reducing build time, improving overall produce-ability, reducing material and treatment costs, and improving our customers’ ability to inspect, prior to use. Our design experience has been gained from direct engagement with customer applications, which means we have a thorough understanding of the practical implications of design decisions on manufacturability, and are in a unique position to help achieve the optimum solution.
Design From Concept Or Specification
Reliance offers a complete front end service for precision mechanical engineering design, from customers’ concepts and specifications. We also help develop concepts and carry out feasibility studies as necessary, depending on the nature of the design. Whatever the preferred approach, we collaborate closely with all our customers and include them in the design review process to achieve the best quality product with the fewest design iterations, allowing products to be brought to market quickly and cost effectively. This approach also means that we are very happy to support customers’ own design programmes where they want to keep design ownership in house, but need support in a specific area such as gear or quadrupole design.
- Across a full concept-to-prototype project
- To fine-tune a project at detailed design stage
- To undertake a design optimisation project
- Design analysis at the end of a design project to assess options for future design iterations.
Diagnostic Investigation
Diagnostic investigation can be a requirement at any point in the product life cycle, but most often we are asked to investigate specific performance issues in the run up to the launch of a new product. At this point time-to-market is a critical factor and the outcome of the analysis a key input into how the launch progresses. The results of any diagnostic investigation are important to commercial and business decision-making, as well as design decisions.A diagnostic programme can include:
- Instrumentation of the mechanism
- Analysis and interpretation of the test data
- Modelling or calculating to investigate possible design solutions
- Rapid manufacture to physically test alternative design solutions
Conclusions and recommendations are discussed at a joint design review with the customer and might include immediate design improvements necessary to meet the essential performance criteria of the specification, design for manufacturing considerations for ease of manufacture and quality/cost improvements, or design options for later revisions of the product.
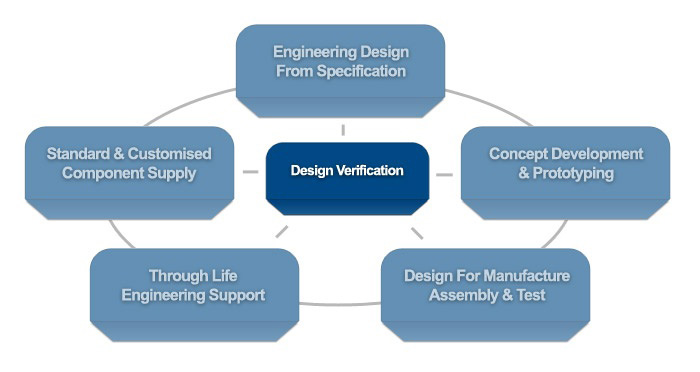
Design Analysis & Validation
Reliance’s design and manufacturing activity, across all our markets, serves customers who make complex performance-critical equipment. All such equipment manufacturers recognise the commercial cost implications of validating the quality and performance of their products. The consequences to the business of poor performance can be significant in terms of failure to meet launch dates, having to repeat the mandatory design approval process with an industry body or third party qualification centre, or even product withdrawal.
Our approach is to integrate design analysis and verification throughout the design process. This allows us to provide the customer’s design team with evidence of the quality/performance of the sub-systems we have designed and manufactured for them.
Activities include:
- Calculations/modelling to re-affirm the design concept
- Ensuring appropriate test interfaces are included in the design
- Designing test fixtures to enable accurate performance testing
- Performance testing of critical parts of the sub-system
- Functional testing of the final assembly
- Preparatory validation testing prior to submission to approved test houses, e.g. vibration, thermal and humidity
A Multi-Disciplined Engineering Team
Professionally qualified design and development engineers from a variety of disciplines.
Scope of Technical Expertise
Our main areas of engineering expertise are diverse but focus on precision instrumentation applications.
Technology Platforms and Customised Solutions
With a technology platform approach we are able to offer a unique combination of design assurance together with the flexibility to tailor it to meet each customer’s own application.
Integrated Design and Manufacture
Our design engineers have first-hand experience of bringing designs into production.
Dedicated Prototyping Facility
Reliance have continually invested in a suite of facilities for product development.
Product Handover and Continuity of Support Through Life
The project is launched into production with the help of the New Project Introduction (NPI) team.
Broad-Ranging Application Experience
Over many years Reliance has worked with a variety of customers in diverse markets.
Product Validation Testing
Our validation test capabilities, which allow us to test, develop and prove designs.
Responsive Design to Secure Market Leadership
An American company with an established, market-leading product line, used Reliance’s design and prototyping capabilities to prove the sales viability of a new feature to enhance the product’s performance. Reliance’s responsiveness and flexibility in design approach provided an effective technical partner for the implementation of its product development strategy.
Technical Innovation to Reduce Costs
A US company, starting a concept design programme for cost reduction, used Reliance’s technical design capabilities to help verify its ideas for innovation. Reliance’s additional capabilities in manufacturing and test provided working prototypes, tested to specification, with detailed performance data to demonstrate the in-service resilience of the design.
Collaborative Design Approach for Product Innovation
Steeper Group, leading provider of innovative prosthetic technology products, embarked on a new product development programme. They faced the challenge of producing a commercially competitive product with the necessary functionality to enable amputees to regain normality, independence and control. The company sought the help of Reliance to provide catalogue parts for the development of their new bebionic hand.