Reliance’s Range of Linear Actuators
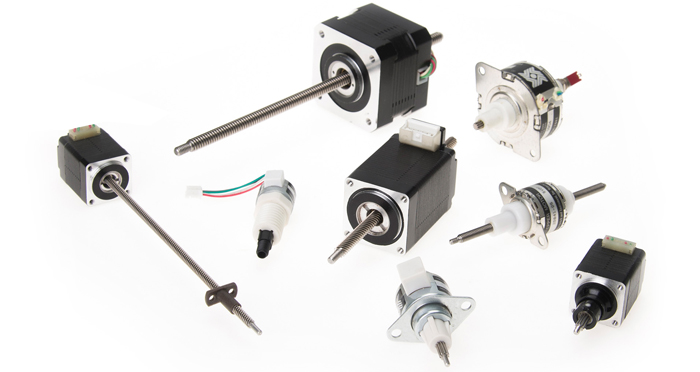
Reliance Precision Limited’s (‘Reliance’) range of Linear Actuators are used in many different applications, across various industry sectors, where high performance, high accuracy and reliability are required.
Reliance offer a full range of sizes from 15 mm to 87 mm in a wide selection of force outputs, across three design formats – captive, non-captive and external. The motorised linear actuators are driven by a stepper motor and integrated leadscrew/nut. The plain shaft is replaced by a leadscrew which is integrated into the rotor of the motor, achieving the rotary to linear conversion directly inside the motor. This approach can greatly simplify the design compared to alternative linear motion solutions, whilst using a thoroughly established technology.
The use of stepper motors also means high resolution and accuracy can be achieved where precision motion is required, as the individual rotary steps of the motor deliver corresponding linear steps of the leadscrew. If positional feedback is required to operate the actuators ‘closed loop’, there are various options available, including home switches, end of stroke proximity sensors and encoders. The stepper motor option also offers high levels of control in comparison to other drive solutions.
Reliance’s actuators have the potential to deliver up to 20 million cycles, and rotary motors can provide up to 25,000 hour’s service. With a choice of two anti-friction coating options, the life of the leadscrew assembly can be extended by up to 300%. The range features two types of motorised linear actuator: Hybrid and Can-Stack.
Hybrid Linear Actuators
Hybrid linear actuators are ideal for applications requiring high resolution positioning and higher levels of axial force alongside long life. These unique hybrid stepper motor linear actuators use a proprietary manufacturing process which incorporates engineering thermoplastics in the rotor drive nut and a stainless steel modified acme leadscrew. This allows the linear actuator to be much quieter, more efficient and more durable than the v-thread and bronze nut configuration commonly used in other linear actuators.
Can-Stack Linear Actuators
Can-stack linear actuators contain a threaded rotor with a leadscrew shaft able to drive linear motion in both directions. The pressed steel body encloses precise internal components, which means this design delivers an economic solution for electrically driven linear motion.
Application Examples:
Medical Devices
Syringe Actuation
The high resolution and repeatability of linear actuators make them perfectly suited to the actuation of syringe pumps.
Example application – Hand-held device for micro-fluidic dispensing
The customer needed to dispense fluid in very small, incremental quantities. With a battery powered, handheld device, the available size, weight and power were limited. Using a miniature, captive style linear actuator to apply pressure onto a bellow, the fluid delivery could be finely controlled within a very small space envelope.
Example application – Desktop instrument for minimally invasive endoscopy
This particular application involved a high backpressure coming from the pump. The actuator needed to provide enough force to actuate the large load and ensure it did not back-drive under the pressure. A suitable frame size, nut selection and lead ensured the syringe could actuate with suitable force and speed. The next step in the application was to adapt a feedback system (through an integrated encoder) which could detect the incorrect usage of the syringe pump. The customer had seen numerous instances of damaged components as the user incorrectly placed the cap on the syringe. The encoder provided position feedback so the software could detect when the syringe was no longer moving, preventing breakages.
Movement of Sample Plates
Actuation of plates containing medical samples can be achieved effectively by linear actuators. Having high-speed capabilities allows fast throughput. High life-expectancy and integrity of the actuators mean they can be left to run continuously.
Example application – Actuation of a 96 well plate
This particular application used two hybrid actuators assembled into an XY stage with a mounting feature for the plate. The low-profile footprint design allowed the customer to keep their instrument size to a minimum, an important requirement for many medical devices.
Loading Cartridges
With the variation of actuators offered, linear actuators can be easily implemented into the majority of cartridge assemblies (the point where a sample/disposable is entered into the machine). Micro-stepping of the actuator ensures smoothness and low noise, providing the sense of quality and integrity at the front end of the machine.
Scientific Instruments & Laboratory Automation
Optics Adjustments
Optical adjustment is perfectly suited to the linear actuator range. The plastic nut technology means no lubrication is required, reducing the risk of contamination. Also, fine resolution, high accuracy and smoothness of motion (generally through micro-stepping) allows clear imaging and reliable results.
Example application – Fine adjustment of optics to change light dispersion in particle size analysis instrument
The main benefit of the actuator within this application was the ability to remotely adjust the optics. The previous arrangement required a service engineer to manually undertake this task. As the customer sold instruments worldwide, it was both time consuming and costly. Having the actuator installed allowed the instrument to be adjusted remotely through the control system.
Example application – Ultra high precision microscope for neuron analysis
This demanding application needed very high accuracy and fine resolution, plus zero backlash. A special high precision leadscrew was selected, along with bespoke internal motor bearings to allow for high vertical loading. The actuator was tested against a competitor and was shown to have superior performance. The axial stiffness of the actuator provided by Reliance was significantly better due to the special preloaded washer/bearing arrangement within the motor.
Precision Actuation for Customer Specific Requirements
Many scientific instruments have bespoke requirements specific to the application. Linear actuators have been used in numerous applications to meet these requirements.
Example application – Water Testing Instrument
This application had numerous actuators working in sync, all coordinating to allow water samples to be measured and tested. Some of the actuators needed to have high force to allow for high pressure within the system, whilst others needed the accuracy and repeatability to ensure doses were consistent.
Printing
Fine Adjustment of Print Nozzles in High Throughput Printers
Automating the adjustment removes the manual task from the operator, allowing it to be done remotely. Generally, these are cost sensitive, so the can-stack range is the most appropriate.
Lifting of Printheads
Due to the high force requirements, lifting of printheads is generally achieved by using large hybrid actuators. In these instances, it is important to have a fine pitch leadscrew to ensure the actuator will not backdrive.
Semi-Conductor
Wafer Measurement Systems
The high-resolution requirements of wafer measurements systems mean the fine adjustment from fine pitch leadscrews are advantageous in these applications. Also, integrated encoders and switches for additional safety and positional feedback are useful.
Wafer Plate Manipulation
Moving of the wafer within an application is generally undertaken through XY stages. Contamination can be an issue in these applications, and is sometimes in a vacuum, so there is often a requirement for special actuators.