Specialist Gears and Rotary Actuation Solutions for Space
View Space ProductsIntroducing Reliance – A Specialist Engineering Company
In 2011 we began our journey to develop our engineering services for the space industry. This was a natural evolution of our longstanding heritage in gears and motion control technology for the terrestrial aerospace sector, combined with over 30 years of building complex vacuum assemblies in a clean environment to meet the needs of the scientific sector. With support from the UK Space Agency and guidance from the European Space Agency (ESA) we have carefully expanded our design and manufacturing facilities and developed our operational processes to meet the stringent requirements of space. Today, components manufactured by Reliance to customer specifications are working on satellites in orbit and we have developed a range of motor gearboxes designed specifically for space.
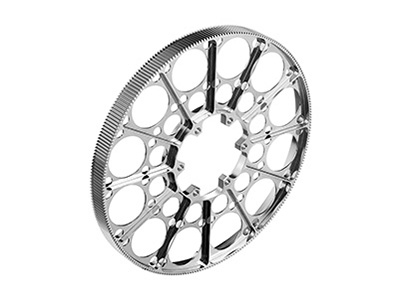
Developing Space Heritage
Learning and adapting
Reliance has progressed through a 5-year product development programme with ESA; from ARTES 3-4 Telecom Newcomers, through ARTES 5.2 Technology Development, to ARTES 3-4 Product Qualification. This measured, conservative path, assisted by Airbus Defence & Space Limited, has enabled us to adapt our established Product Assurance processes in line with space requirements. We have developed our design knowledge and our operational skills and facilities with regard to space – in materials and process control, in environmental testing, in tribology, in cleanliness disciplines, and in designing products for high vibration, long-life applications.
Research and development
To further Reliance’s specialist gear expertise in relation to space we have undertaken CEOI-ST funded research into low speed tribology, in collaboration with ESTL. Test rig development expertise has also been further developed via a collaborative technology project with Oxford Space Systems, jointly funded by NATEP (National Aerospace Technology Programme).
Sharing knowledge
Reliance is one of the founding members of the UK Space Mechanisms Working Group, having chaired the group between 2013 and 2015. This forum provides a valuable link between mechanisms experts from the satellite primes, smaller industrial and research organisations and academic institutions, together with Innovate UK. The group also has links to the UK Space Agency and ESA which provides a strong foundation for sharing knowledge between the agencies and industry.
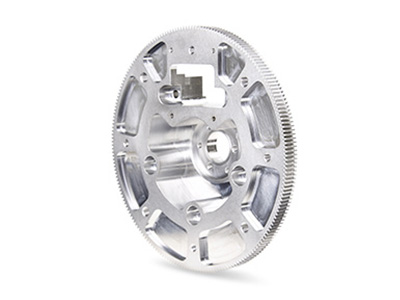
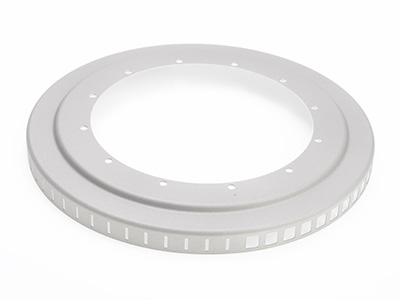
Evidencing quality
Reliance has supplied bespoke components, manufactured to customer specifications, which are now in orbit in satellite mechanisms or part of current build programmes. These include gears and other complex components with demanding manufacturing tolerances and features. Delivering these projects successfully has enabled Reliance to evidence that the company has the necessary Product Assurance procedures to supply high-quality parts, to drawing and defect-free.
Developing new products
Reliance has made a successful transition from terrestrial aerospace to space in our approach to new product development. We have undertaken a number of customer specific concept designs, taking two motor gearbox projects through detailed development, manufacture, assembly, test and into qualification for use in space mechanisms. These products have been designed by Reliance and are manufactured in the UK, providing proven building blocks for future customers.
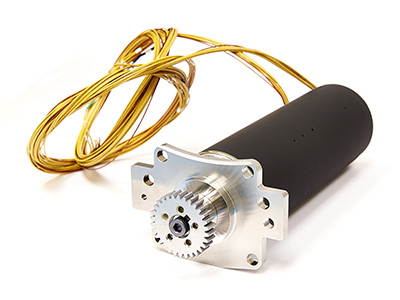
Euro SMG
This 51 mm OD Stepper Motor Gearbox has been developed under ESA’s ARTES programme (‘EuroSMG‘). It has been designed for a high-power telecoms satellite application, with the requirements specified by Airbus Defence & Space Limited.
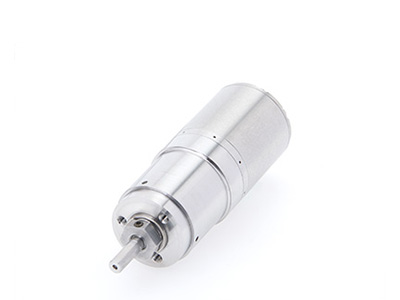
Compact SMG
This 25 mm OD Stepper Motor Gearbox has been developed under the UK Space Agency’s NSTP3 programme. It has been designed for a commercial earth observation satellite application, with the requirements specified by Surrey Satellite Technology Limited.
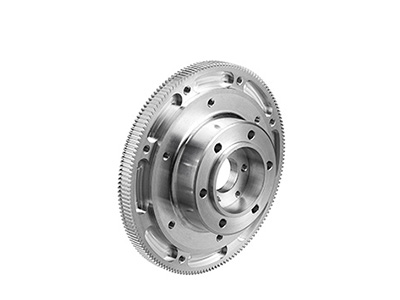
Satellite Gears
Reliance supplies bespoke gears and complex components for use in space mechanisms such as solar array drive mechanisms and antenna pointing mechanisms. Our gears have flight heritage in a range of satellites currently in orbit.
Space Project Case Studies
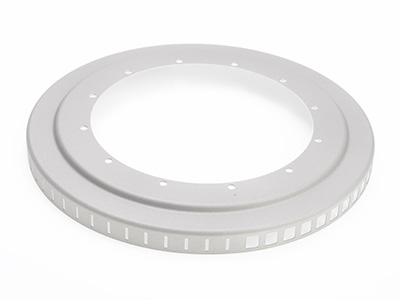
Bespoke components for telecom satellite mechanisms
The component shown is used by Airbus Defence & Space Limited on their highly successful Eurostar3000 satellite platform. This thin-walled component, when combined with the properties of the material used, is highly unstable during manufacture. Its complex features must be machined to micron-level tolerances, followed by an aggressive surface treatment to produce the necessary surface finish. Each component must be made to a measured, repeatable standard, with no inconsistencies. Following initial development trials, Reliance has consistently supplied this delicate part completely defect-free, a critical requirement for our customer.
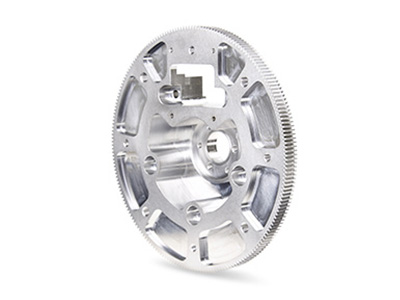
Gears for earth observation satellite mechanisms
Surrey Satellite Technology Limited (SSTL) is well known for: “Changing the economics of space”, with Commercial-Off-The-Shelf (COTS) products being an essential part of delivering the company’s commercial objectives. Reliance supplies gears from our standard catalogue range, modified to suit SSTL’s requirements, together with custom gears manufactured to their design, providing a complete end-to-end gear package for use in SSTL’s Antenna Pointing Mechanism (APM). The gear shown has been supplied since 2013 and is currently working in orbit as part of a number of earth observation missions.
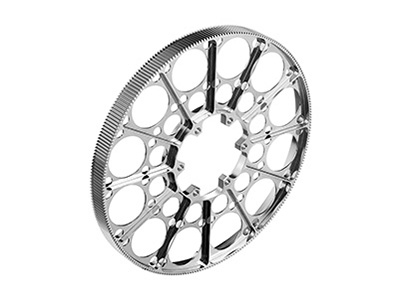
Bespoke gears for scientific satellite mechanisms
Reliance was part of the supply chain for the successful 2014 Rosetta science mission to investigate Comet 67P/Churyumov–Gerasimenko. Specialist gears were manufactured to a Kongsberg Defence & Aerospace design, for use within their Solar Array Drive Mechanism (SADM). The SADM was built into the satellite platform, supplied by Airbus Defence & Space Limited, which was launched in 2004 under the European Space Agency’s Rosetta programme. This custom-built gear is an example of complex machining, where a significant proportion of material had to be removed to reduce the weight of the gear, whilst still maintaining the necessary accuracy to ensure the gear’s performance
Design and Validation
Collaborative engineering
Reliance has worked as a collaborative technical partner on a range of programmes to support designers responsible for both new and mature products. We provide a complementary design capability, offering access to specialist facilities and technical expertise, or additional capacity during resource intensive projects. The scope and depth of design support is tailored to suit each customer’s in-house expertise and resource levels, managed flexibly in line with their design, manufacturing and organisational practices. We have a professional multi-disciplined engineering team with hands-on product implementation experience, capable of undertaking: • Design from specification • Concept development and prototyping • Collaborative design review • Through-life engineering support
Skills and capabilities
We cover a broad range of disciplines, including mechanical, electronic and control engineering, with a core design expertise in complex geared components and high performance geared assemblies. Co-location with our production facility helps secure effective design implementation, whilst unique test and validation capabilities provide customers with confidence in the quality and performance of their equipment, securing effective market launch and reducing through-life costs. We offer practical experience in bringing product designs into production, with design engineers working alongside production engineers and operations teams at Reliance’s UK manufacturing facility.
Metrology, test and design verification
Providing essential data to our customers to validate the functional performance of their design, including: • Custom designed test equipment and software • Specialist gear and gearbox test rigs • Temperature, humidity and vibration testing • Metrology data at component and assembly level Design verification as a standalone investigative project or as part of a design engineering project, ensuring critical time-to-market deadlines are secured by: • Design analysis by calculation/modelling • Performance validation of critical design elements • Assessment of alternative design solutions • Functional testing of the final assembly
Manufacturing and Assembly
Continuous improvement
We are engaged in business process improvement activities and invest £2 million annually to ensure that we keep our precision machining and metrology capabilities at the forefront of the manufacturing industry. Reliance supplies concession-free components and fully tested assemblies for use directly into final production, helping our customers reduce supply chain management costs. We provide a single point of contact for the supply of critical sub-systems, combining our own manufactured and bought-in parts, together with our customers’ preferred suppliers. By working collaboratively we have demonstrated that we are able to respond effectively to our customers’ plans for growth and support their supply chain strategies effectively.
Ensuring production yield
Contamination control is vital to production yield. It is essential to provide the most appropriate assembly environment for projects with different cleaning procedures and different sensitivities to contaminants. Reliance has a suite of cleanrooms, each established to support particular needs of customer projects from a range of markets, including scientific instruments and aerospace and defence. To prevent cross-contamination and ensure the necessary disciplines and procedures are adhered to, a separate clean area for space has been introduced.
Component manufacturing and clean assembly
High accuracy manufacturing facility with embedded through-process quality control to ensure full compliance to specification: • High precision manufacture of critical components • World-class, NPL accredited, metrology capability • Tailored cleaning processes to customer specification • Bespoke packaging and supply options Assembly of high performance sub-systems where the avoidance of contamination is critical to achieving demanding accuracies: • ISO 7/Class 10,000 clean area – space procedures • ISO 7/Class 10,000 cleanroom – optics handling • ISO 6/Class 1,000 cleanroom – oil and grease-free • ISO 4/Class 10 flexible laminar flow cabinets
New product introduction
Experienced engineering team responsible for the smooth transition from design to manufacture: • Close customer liaison and project management • Highly disciplined build standard control • Production engineering “design-for-manufacture” • Development of manufacturing methods and tooling
Quality and Product Assurance
Trust and experience
With over 60 years’ experience in serving the aerospace and defence sectors Reliance is able to demonstrate consistent achievement of the stringent performance criteria required by these industries. This is further strengthened by successful audits and product supply to space primes and recognition from ESA. We have built longstanding relationships with major OEMs, systems integrators and prime contractors.
Disciplined and adaptable
We ensure a consistent approach based on established operational disciplines and methods, and thorough build standard control. This allows us to manage effectively a combination of in-house designed and manufactured elements and externally sourced components, including those from both our own and our customers’ supply chains. Our size and independence means that we can adapt to the needs of our customers’ organisations and adopt their operational procedures alongside our own systems. A strong project management approach, drawing upon operational experience and close customer collaboration, ensures that major new projects are introduced into production with confidence, helping to reduce time to market for new products.
Quality assured
As a BS EN ISO 9001 and AS9100 approved company, Reliance is committed to providing high standards in product and service delivery. We adhere to the stringent quality and product assurance requirements set out by our space customers, with tightly controlled operational processes and IT systems in place to evidence all activities throughout production. We welcome all new customers to visit our facility in Huddersfield and witness our systems and procedures.
Quality control
Effective application of metrology and test is a core part of our company philosophy. Inspection and measurement disciplines are embedded throughout the component manufacturing process in order to prove parts are manufactured correctly to specification. Investment in test engineering has resulted in unique facilities for functional testing of assemblies, with the capability to custom-design test equipment and processes for different applications and performance criteria.
Creativity and problem solving
Reliance is committed to developing knowledge and understanding and has a strong appetite for problem solving. By understanding the issues facing our customers – technically, operationally and commercially – we are able to provide creative technical solutions. Our creativity is grounded firmly by our core company principle which demands that we can prove that our design and manufacturing solutions meet the customers’ specifications and performance criteria.